半导体概念股
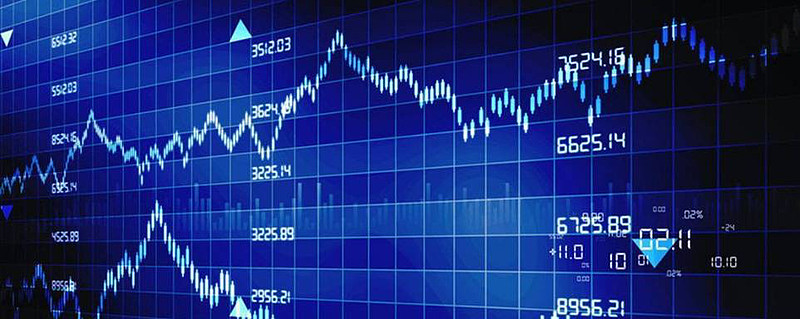
本篇是系列第三篇,主要讲湿电子化学品、CMP材料和靶材。下一篇开始介绍大家庭内的上市核心公司。
3.5、湿电子化学品:保证工艺精度的重要材 料,国产替代任重道远
湿电子化学品又称工艺化学品,是微电子、光电子湿法工艺(主要包括湿法刻蚀、湿法清洗)制程中使用的各种液体化工材料。湿电子化学品按照大类一般可划分为通用化学品(通常为超净高纯试剂)和功能性化学品。湿电子化学品主要用于半导体、光伏太阳能电池、LED 和平板显示等电子信息产品的清洗、蚀刻等工艺环节。
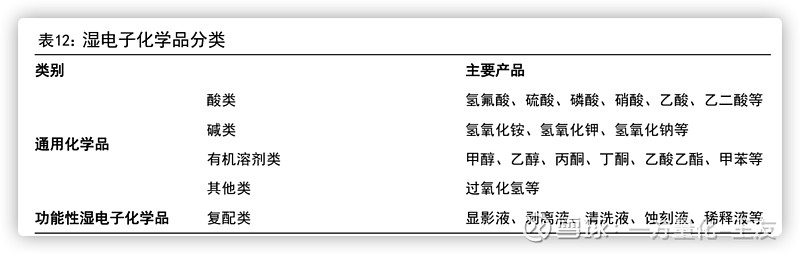
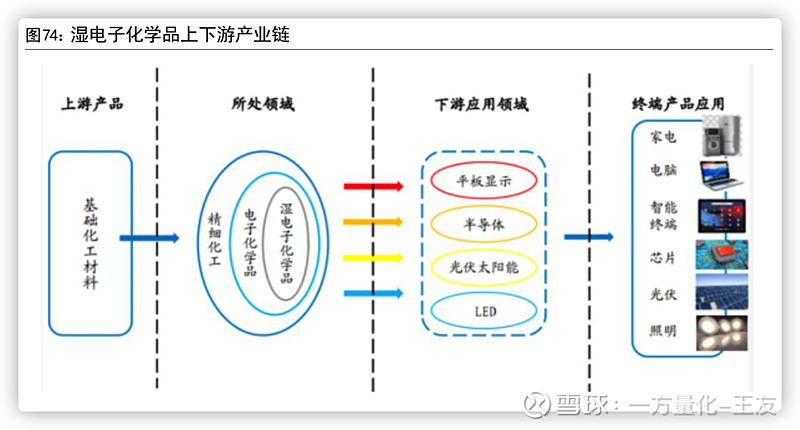
半导体行业由于精细加工要求,对湿电子化学品要求更高。SEMI 将半导体用湿电子化学品按金属杂质、控制粒径、颗粒个数和应用范围等指标制定国际 5 个等级分类标准。不同线宽的集成电路制程工艺中必须使用不同规格的超净高纯化学品进行蚀刻和清洗,且湿电子化学品的纯度和洁净度对集成电路的成品率、电性能及可靠性均有十分重要的影响。
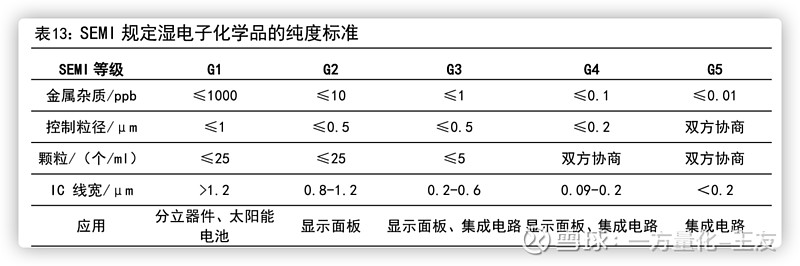
超净高纯试剂是湿电子化学品的重要组成部分,占比 88.2%。超净高纯试剂按照性质划分可分为:酸类、碱类、有机溶剂类和其它类,主要包括双氧水、氢氟酸、硫酸、磷酸、盐酸、硝酸、氢氧化铵等。根据中国电子材料行业协会统计,湿电子化学品中占比较高的是双氧水(18.9%)、氢氟酸(18.1%)、硫酸(17.3%)、硝酸(16.2%)等;在半导体加工领域,需求量较大的产品是硫酸(32.8%)、双氧水(28.1%)、氨水(8.3%)、主要应用于晶圆的清洗环节。
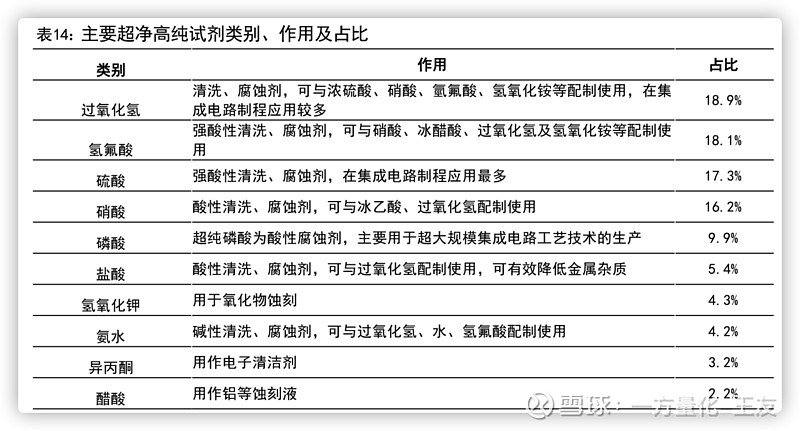
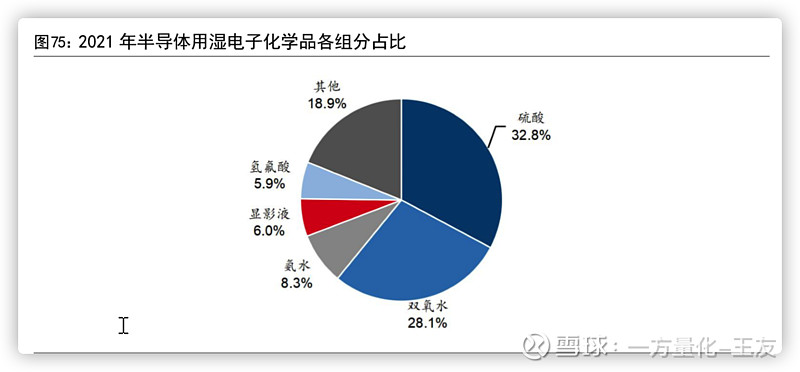
全球湿电子化学品市场规模稳步增长,2025 年需求量增加 50%以上。根据智研咨询数据,全球湿电子化学品市场规模 2011 年为 25.3 亿美元,2020 年为 56.8 亿美元,2011-2020 年 CAGR 值 9.4%。需求量方面,根据中国电子材料行业协会数据,2021 年全球湿电子化学品需求量为 458.3 万吨,半导体需求量 209 万吨,显示面板需求量 167.2 万吨,光伏等其他需求量 82.1 万吨。预计到 2025 年全球湿电子化学品需求量将达到 697.2 万吨,半导体需求量 313 万吨,显示面板需求量 244 万吨,光伏等其他需求量 140.2 万吨,总需求量将增加 50%以上。
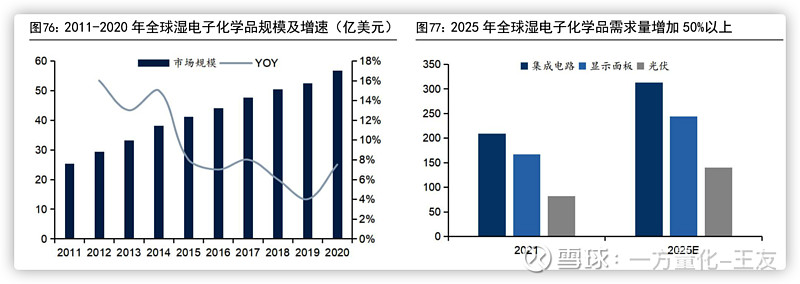
湿电子化学品中国市场快速增长,2025 年需求量超过 70%。中国湿电子化学品市场规模 2011 年为 27.8 亿元,2021 年为 137.8 亿元,CAGR 值 17.3%,高于全球平均增速,预计 2022 年将达到 163.9 亿元,2028 年将达到 301.7 亿元。2021 年中国湿电子化学品需求量为 213.5 万吨,半导体需求量 70.3 万吨,显示面板需求量 77.8 万吨,光伏需求量 65.4 万吨。预计到 2025 年中国湿电子化学品需求量将达 到 369.6 万吨,半导体需求量 106.9 万吨,显示面板需求量 149.5 万吨,光伏需 求量 113.1 万吨,总需求量超过 70%。
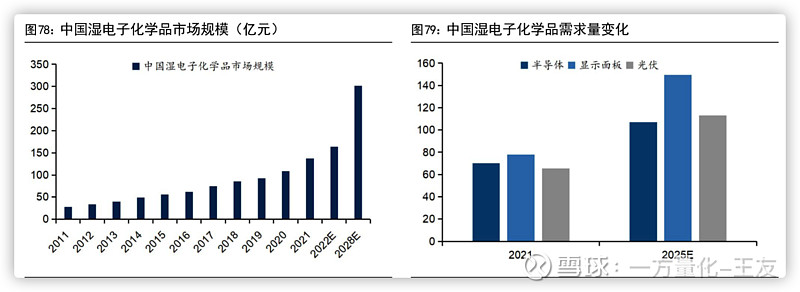
晶圆厂扩产刺激湿电子化学品材料需求。8 吋及 12 吋产能扩张带动高纯试剂需求进一步提升,12 吋晶圆制造过程中所使用的湿电子化学品约为 24 千克/片,8 吋 晶圆消耗量约为 12 吋晶圆消耗量的五分之一,约为 5 千克/片左右,6 吋晶圆消耗量约为 12 吋晶圆消耗量的八分之一左右,约为 3 千克/片。

中美贸易摩擦,推动湿电子化学品国产替代进程。湿电子化学品在全球半导体市场规模占比 6.7%,约 20 亿美元,国内市场规模约 6 亿美元。在湿电子化学品的主要应用中,半导体用湿电子化学品国产化率较低,约为 20%,显示面板国产化率约为 40%,具有广阔的国产替代空间。近年中美贸易持续摩擦,会对电子材料的供应格局产生一定影响,刺激湿电子化学品的国产替代需求,推动国产替代进程。
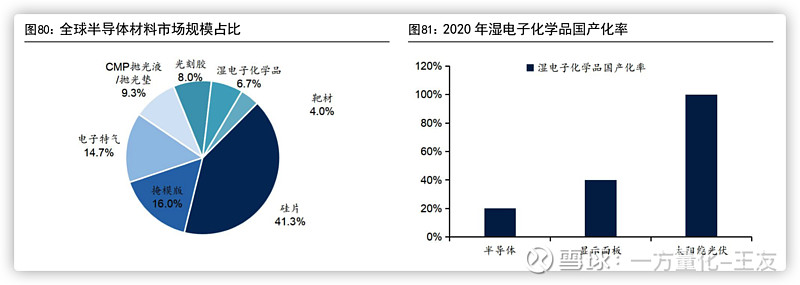
目前全球范围内从事湿电子化学品研究开发及大规模生产的厂商主要集中在美国、德国、日本、韩国、中国台湾等地区。主要企业包括德国巴斯夫、美国亚什兰化学、Arch 化学,日本关东化学、三菱化学、京都化工、住友化学,中国台湾新林科技,韩国东友精细化工等。前瞻产业研究院数据显示 2019 年中国国内在国内湿电子化学品市场供应分布仅占 9%,欧美企业和日本企业占比超过 60%。
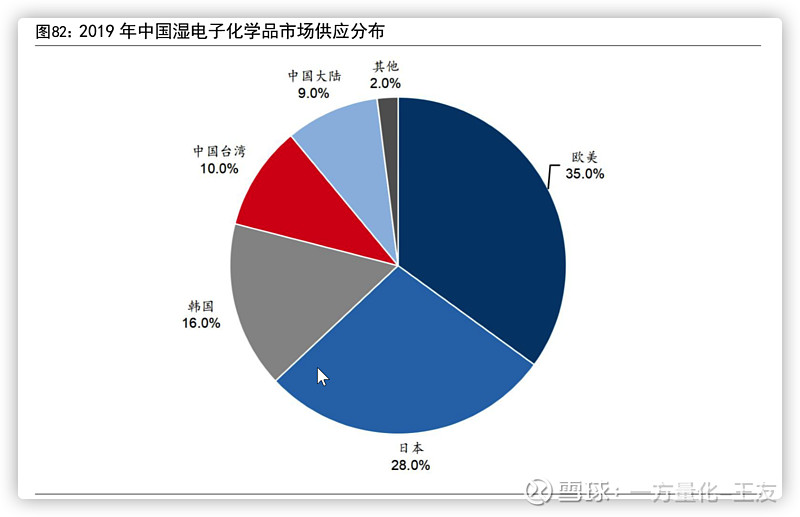
我国湿电子化学品多集中于低端市场,高端市场亟需突破。国内湿电子化学品主要供应光伏市场、低代线平板显示市场和 6 寸及以下半导体市场,G6、G8 代线平板显示和 8 寸及以上半导体市占率仅为 10%。我国湿电子化学品由于起步较晚,品类丰富度及提纯技术水平相对落后于国外领先企业,因此多集中于低端市场,但国内厂商积极开拓高端湿电子化学品市场,头部厂商已具备了生产 G4、G5 标准的部分湿电子化学品品类的能力,同时结合运输、价格和售后等方面的本土化优势,未来湿电子化学品的高端市场国产替代空间广阔。
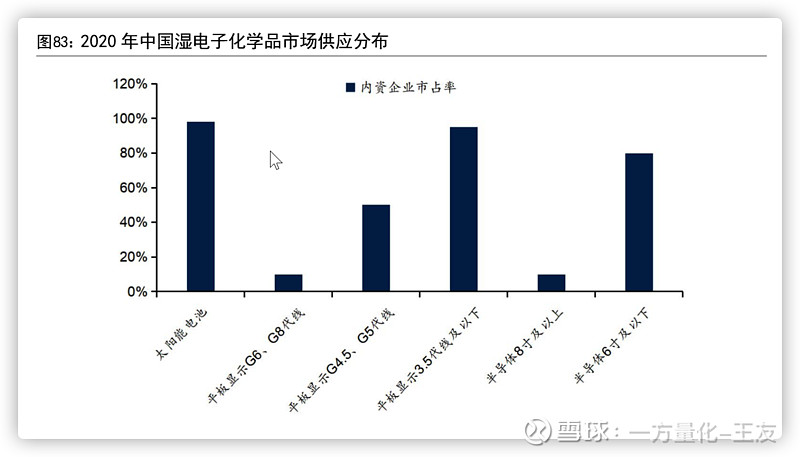
3.6、CMP 材料:抛光液&抛光垫,平坦化技术核心材料
CMP 是一种化学腐蚀和机械研磨相结合的平坦化半导体表面工艺,是集成电路晶圆制造中实现晶圆全局均匀平坦化的关键工艺。半导体制造分为前道工艺和后道工艺,其中前道工艺指在晶圆上形成器件的工艺过程,也称晶圆制造,后道工艺指将晶圆上的器件分离,封装的工艺过程。前道工艺共有七大工艺步骤,分别为氧化/扩散、光刻、刻蚀、离子注入、薄膜生长、清洗与抛光、金属化,通过循环重复上述工艺,最终在晶圆表面形成立体的多层结构,实现整个集成电路的制造。
半导体概念股
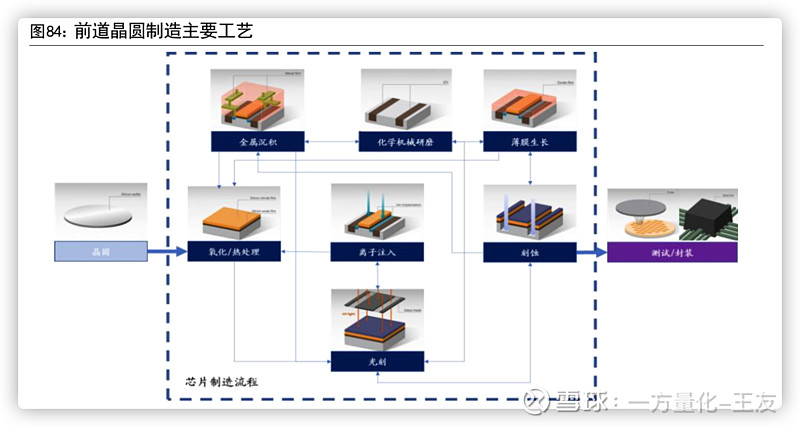
在晶圆制造的各个阶段,晶圆表面都要进行平坦化处理以保持完全平坦。目的是去除多余的材料,或者是为了建立极其平坦的基底,以便添加下一层电路特征。如果晶圆制造过程中无法做到纳米级全局平坦化,既无法重复进行光刻、刻蚀、薄膜和掺杂等关键工艺,也无法将制程节点缩小至纳米级的先进领域,因此随着超大规模集成电路制造的线宽不断细小化而产生对平坦化的更高要求需求,CMP 在先进工艺制程中具有不可替代且越来越重要的作用。
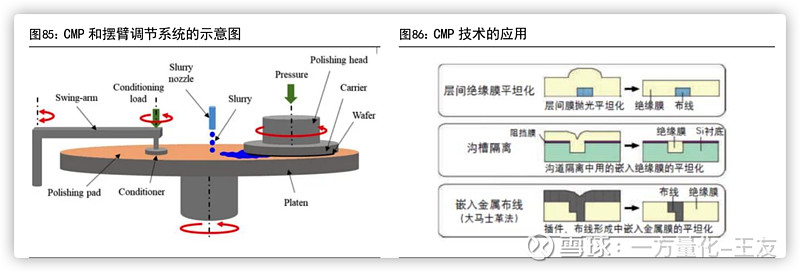
CMP 抛光垫和抛光液是化学机械抛光环节的核心耗材。CMP 工艺过程中涉及的耗材包括:抛光机、抛光液、抛光垫。根据 SEMI 2018 年数据,CMP 抛光材料在集成电路制造材料成本中占比 7%,其中 CMP 抛光垫、CMP 抛光液、CMP 清洗液分别占比 33%、49%、5%,合计占 CMP 抛光材料成本的 85%以上。
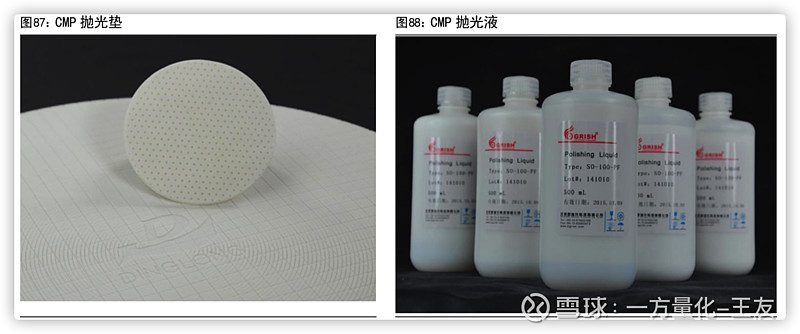
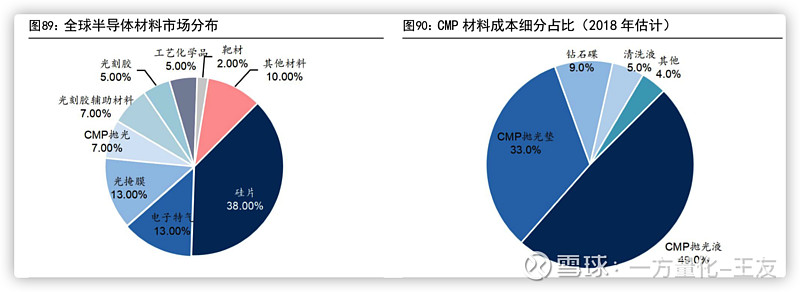
全球晶圆厂积极扩产提升 CMP 材料需求。根据国际半导体协会 SEMI 数据,2021 年全球晶圆制造材料市场同比增长 15.5%,达到 404 亿美元,晶圆封装材料市场规模同比增长 16.5%,达到 239 亿美元。硅、湿化学品、CMP 和光掩模领域在晶圆制造材料市场中增长强劲。
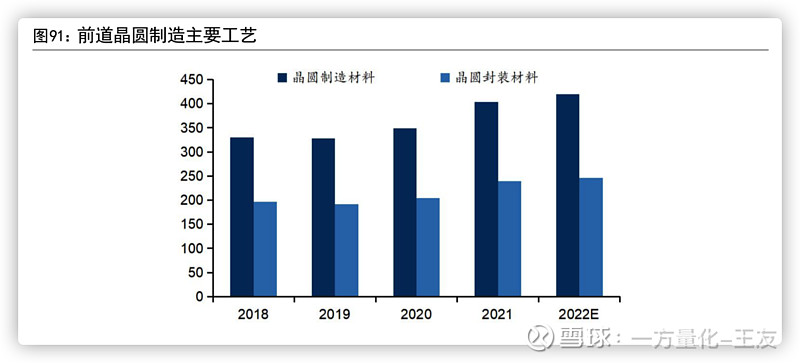
晶圆制程缩小需大幅提高 CMP 次数,导致 CMP 抛光耗材在晶圆制造过程中消耗量增加。根据 Cabot 微电子数据,14 纳米以下逻辑芯片工艺要求的关键 CMP 工艺将达到 20 步以上,使用的抛光液将从 90 纳米的约 5 种抛光液增加到 20 余种,种类和用量迅速增长; 7 纳米及以下逻辑芯片工艺中 CMP 抛光步骤甚至可能达到 30 步,使用的抛光液种类接近 30 种。CMP 的应用边界,从最初的 STI(浅沟槽隔离层)拓展到 ILD(层间介质)、Metal(金属互连层)、TM(顶层金属)等。
目前逻辑芯片正向 7nm 以下先进制程发展,台积电 5nm 产品已于 2020 年下半年实 现量产出货,而芯片制程从成熟制程 28nm,先进制程 14nm 上升到 7nm 后,CMP 抛光步骤大幅增加。
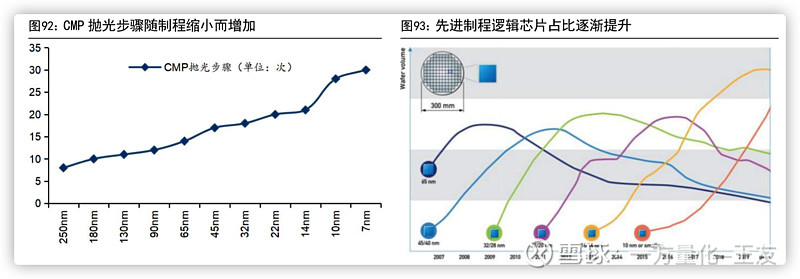
存储芯片的封装工艺进步,让 CMP 工艺从前道延展到后道。存储芯片由 2D NAND 向 3D NAND 技术变革,也会使 CMP 抛光步骤数近乎翻倍。集成电路 2D 存储器件的线宽已接近物理极限,NAND 闪存已进入 3D 时代。随着系统级封装等新的封装方式的发展,技术实现方法上出现了倒装、凸块、晶圆级封装、2.5D 封装和 3D 封装等先进封装技术。目前 64 层 3D NAND 闪存已进入大生产,232 层闪存已经推出,目前处于扩产周期。
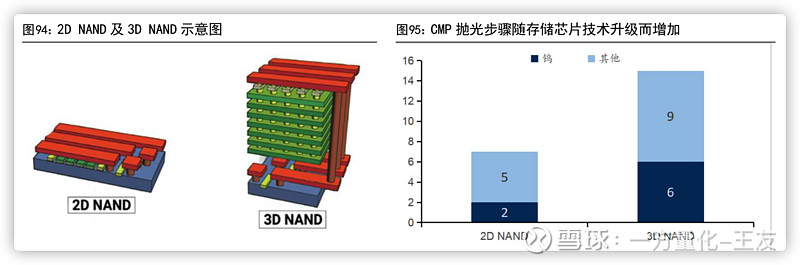
抛光垫:抛光垫的自身硬度、刚性、可压缩性等机械物理性能对抛光质量、材料去除率和抛光垫的寿命有着明显的影响。硬度即定期保持形状精度的能力,采用硬质抛光垫可以获得较好的工件平面度,使用软质抛光垫可以加工变质层和表面 粗糙度都很小的抛光平面。可压缩性决定抛光过程中抛光垫和工件表面的贴合程度,影响材料去除率和表面平坦化程度。可压缩性越大,贴合越紧密,去除率越高。目前,国际先进厂家在 3D-NAND 等高要求的生产环节中应用固定研磨颗粒的抛光垫,其产品融合了原本存在于抛光液的抛光颗粒,抛光垫重要性有望进一步提高。
CMP 抛光垫行业具有技术密集、资金密集、客户验证壁垒高的特点,导致抛光垫全球市场集中度高,主要被陶氏化学占据,占全球 79%的市场份额,美日 5 大厂 商占据 91%的份额。过去,国内抛光所用 CMP 抛光垫,几乎全部依赖进口。目前中国国内仅鼎龙股份有能力大批量提供,是国内唯一一家全面掌握抛光垫全流程 核心研发和制造技术的 CMP 抛光垫供应商。目前陶氏化学垄断了中国近 90%的 CMP 抛光垫市场供给,是国产替代的主要对象。
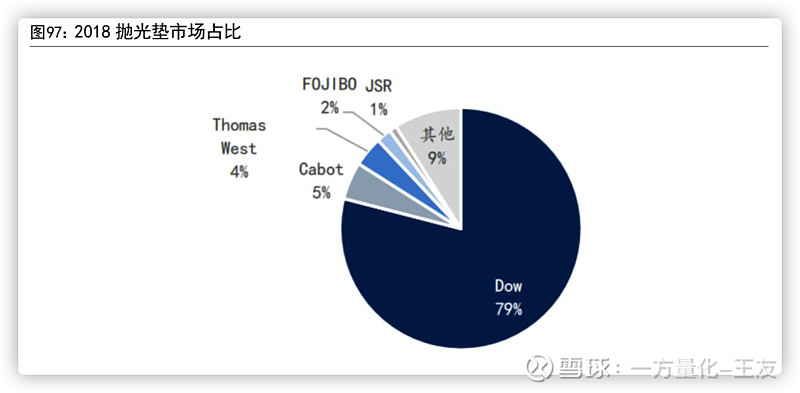
抛光垫行业的壁垒主要包括:技术壁垒、专利壁垒和客户认证壁垒。技术上,抛光垫需要持续试错,形成稳定有效的材料配方、制作工艺及设计图案,从而获得较好的抛光速率和抛光效果,在各项指标上达到较好的平衡。
抛光液:抛光液由去离子水、磨料、PH 值调节剂、氧化剂以及分散剂等添加剂组成。在抛光过程中,抛光液中的氧化剂等成分与硅片表面材料产生化学反应并在表面形成化学反应薄膜,后由抛光液中的磨粒在压力和摩擦的作用下将其去除,从而实现抛光。根据应用环节、配方中磨粒、PH 值的不同,抛光液可以进行不同 分类。
按照应用环节分类:可分为硅抛光液、铜抛光液、阻挡层抛光液、钨抛光液、钴抛光液、介质层(TDL)抛光液、浅槽隔离(STI)抛光液和硅通孔(TSV)抛光液。
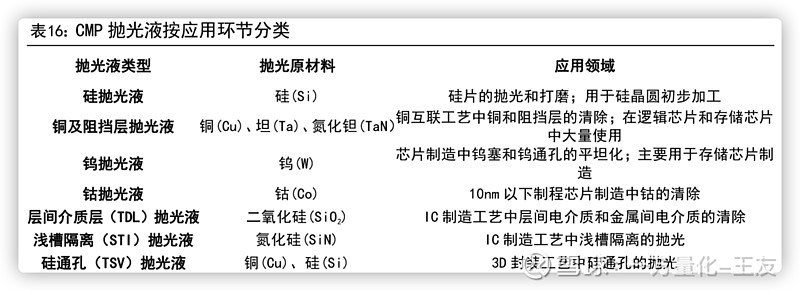
按照配方中磨粒分类:可分为二氧化硅、氧化铈、氧化铝磨粒等。二氧化硅磨粒优点是活性强、易于清洗、分散性及选择性好,多用于硅及层间氧化硅介电层的抛光,缺点是硬度大,容易对硅片表面造成损伤,且抛光效率低;氧化铝磨粒优点是抛光效率高,缺点是硬度大、选择性低、易出现团聚,因此抛光液中常需加 入各类稳定剂和分散剂,导致成本上升;氧化铈磨粒优点是硬度低,抛光效率高,平坦度高,清洁无污染,缺点是团聚严重,需加入各类稳定剂和分散剂,且铈属于稀有金属,成本偏高。
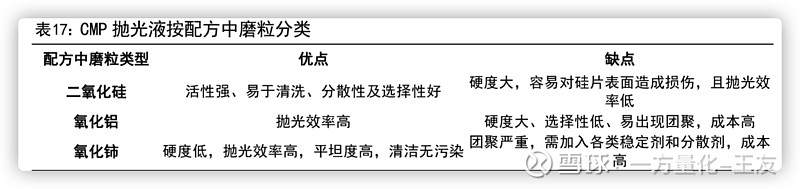
按照 PH 值分类:可分为酸性抛光液和碱性抛光液。酸性抛光优点是抛光效率高、可溶性强,多用于对铜、钨、铝、钛等金属材料进行抛光,缺点是腐蚀性强导致选择性低,易降低抛光设备的寿命及可靠性,所以需要在抛光液中添加抗蚀剂 (BTA)提高选择性,但 BTA 对抛光液的稳定性会造成一定影响;碱性抛光液优点是腐蚀性低、选择性高,多用于抛光硅、氧化物及光阻材料等非金属材料的抛光,缺点是抛光效率较低,原因是不容易找到在弱碱性中氧化势高的氧化剂。

抛光液在材料成本中占比最高。根据 SEMI 数据,全球 CMP 材料成本占比中,抛光液用量最大,其中抛光液占比 49%,抛光垫占比 33%,合计占比 82%,钻石碟占比 9%,清洗液占比 5%。根据 Cabot Microelectronics 和 TECHCET 数据,全球 CMP 抛 光液 2016 年市场规模为 11 亿美元,2021 年为 18.9 亿美元,2016-2021 年 CAGR 值为 11.4%。预计 2026 年将达到 25.3 亿美元。
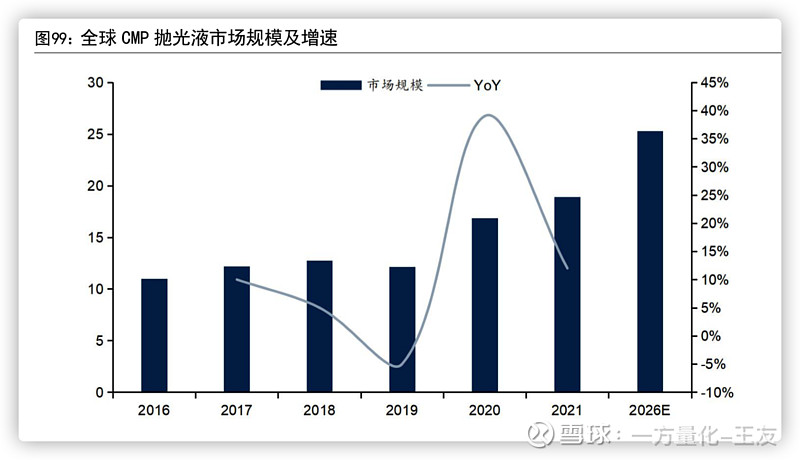
根据观研天下数据,2018 年 TOP5 厂商为 CabotMicroelectronics、Versum、日立、富士美、陶氏,合计占市场 80%以上市场份额。然而抛光液市场格局有分散化趋势,国产替代机会更大。美国的 CabotMicroelectronics 是全球抛光液市场龙头,2000 年市占率高达 80%,不过到 2017 年 CabotMicroelectronics 全球市占率降低 至 36%。其他主要供应商包括 Hitachi、Fujimi、Versum 等,市占率分别为 15%、11%、10%。抛光液市场分散程度相对较高,多元化发展趋势明显,国产厂商实现替代机会较大。目前安集微电子已经形成替代,但全球市占率仅有 2%。
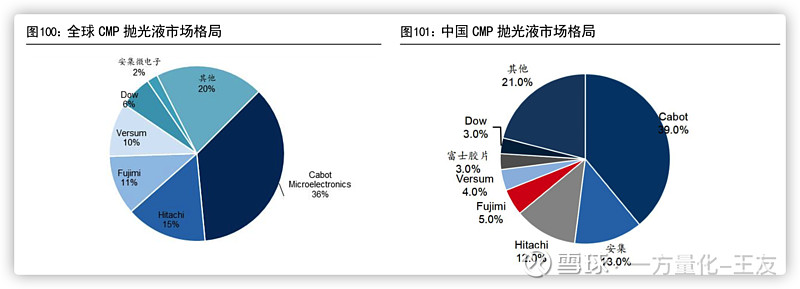
国内厂商加快验证周期。核心客户认证体系壁垒方面,由于抛光垫和抛光液对芯片良率影响较大,但成本占比较相对较低,在稳定而成熟的 FAB 厂中,为确保芯片良率,一般很少替换原有稳定的供应商。半导体 Fab 厂具有资本密集和技术密 集的属性,对于上游半导体原材料的稳定性和良品率有极高的要求,因此对于原材料供应商认证门槛极高、认证周期较长。目前在半导体产业链安全可控的大环 境下,国内厂商速度加快,验证周期缩短到半年左右。
3.7、靶材:PVD 沉积核心材料,薄膜沉积重要组成部分
靶材是 PVD 的核心材料。物理气相沉积(Physical Vapor Deposition)技术是制备电子薄膜材料的主要技术之一,是利用物理方法在基板表面沉积薄膜的方式,根据沉积方式的不同,PVD 分为溅射法和蒸镀法,被沉积的材料称为靶材。靶材是 PVD 的核心材料。
溅射法是利用离子源产生的离子,在真空中加速聚集成高速离子流,轰击固体表面,离子和固体表面的原子发生动能交换,使固体表面的原子离开靶材并沉积在基材表面,从而形成纳米(或微米)薄膜。被轰击的固体是 PVD 沉积薄膜的原材料,称为溅射靶材。靶材质量的好坏对薄膜的性能起着至关重要的决定作用。
真空蒸发镀膜是指在真空条件下,利用膜材加热装置(称为蒸发源)的热能,通过加热蒸发某种物质使其沉积在基板材料表面的一种沉积技术。被蒸发的物质是用真空蒸发镀膜法沉积薄膜材料的原材料,称之为蒸镀材料。真空蒸发镀膜技术具有简单便利、操作方便、成膜速度快等特点,主要应用于小尺寸基板材料的镀膜。
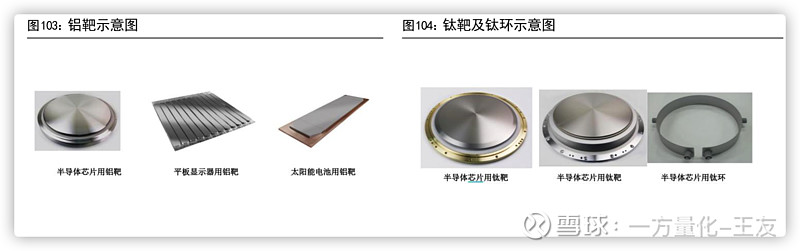
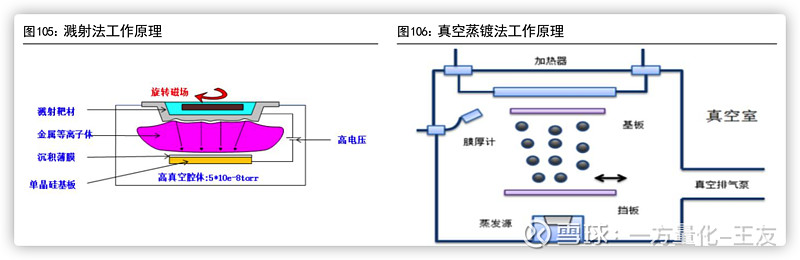
按照应用不同、化学成分不同、形状不同,靶材产品有三种分类方式。按下游应用可分为半导体靶材、平面显示靶材、太阳能靶材和其他类;按形状不同可分为长靶、方靶和圆靶;按照化学成分不同,可分为金属靶材、化合物靶材和合金靶材。
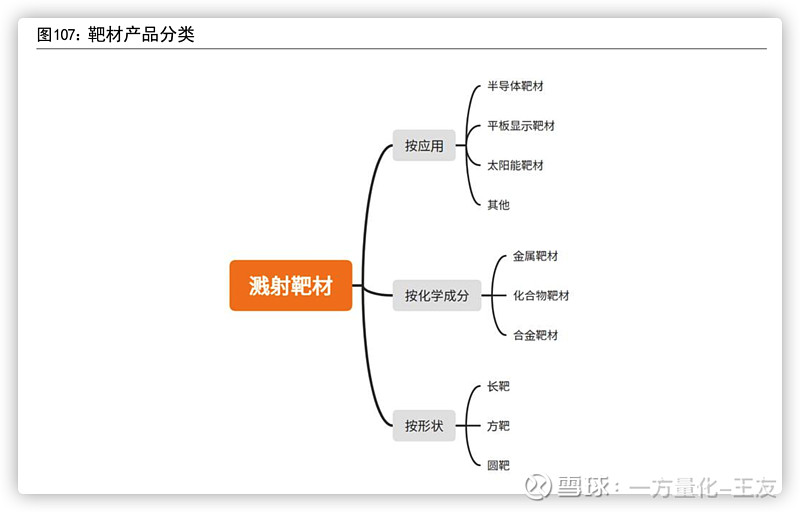
靶材产业链可以分为金属提纯、靶材制造、镀膜和终端应用四个环节。首先是金属提纯,原材料铝、铜、钽、钛等金属以金属提纯方式形成高纯金属,作为靶材制造的原材料;第二环节是靶材制造,将高纯金属通过加工形成溅射靶材,制造好的靶材包括靶坯和背板两部分,靶坯是溅射靶材的主体,背板起固定靶坯的作 用。第三个环节是镀膜,以溅射镀膜为例,以高速离子束流轰击靶坯,溅射出靶 坯表面原子,沉积于基板从而制成电子薄膜,电子薄膜按照应用不同有不同分类; 最后将薄膜材料应用于半导体芯片、平板显示器、信息存储、光学元器件、薄膜太阳能等不同领域。
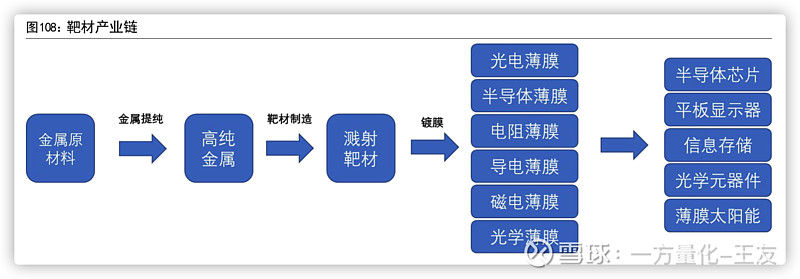
靶材市场主要分布于平板显示、记录媒体、太阳能电池和半导体四大领域,其中半导体占比约 10%。根据华经产业研究院数据,截至 2021 年,四大领域靶材市场占比约 94%,其中平板显示、记录媒体和太阳能电池占比较高,分别为 34%、29% 和 21%,半导体占比约10%。
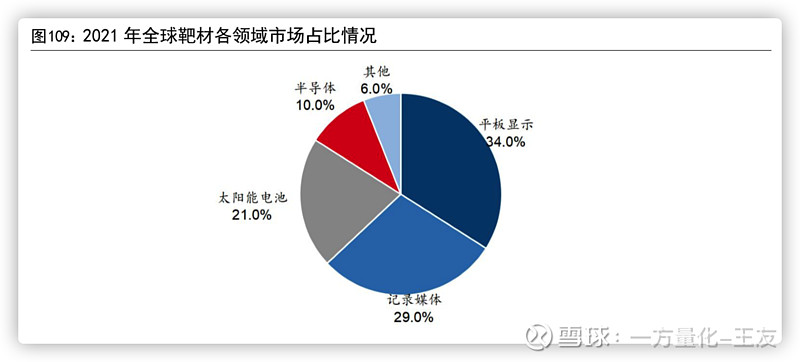
根据 SEMI 数据,全球半导体靶材市场规模整体保持增长态势。2021 年为 16.95 亿美元,同比增长超过 20%,其中晶圆制造用靶材 10.5 亿美元,封装用靶材 6.45 亿美元。根据智研咨询数据,2021 年中国半导体靶材市场约,预计 2022 年中国半导体靶材的市场规模将达到 75.1 亿元,同比增长 19%,2018-2022 年,中国半导体靶材市场规模一直保持较快增速,CAGR 值为 22.1%。一方面系消费电子、5G、新能源等半导体下游应用快速发展,另一方面由于国内政策推动了半导体产业进 一步向国内转移。
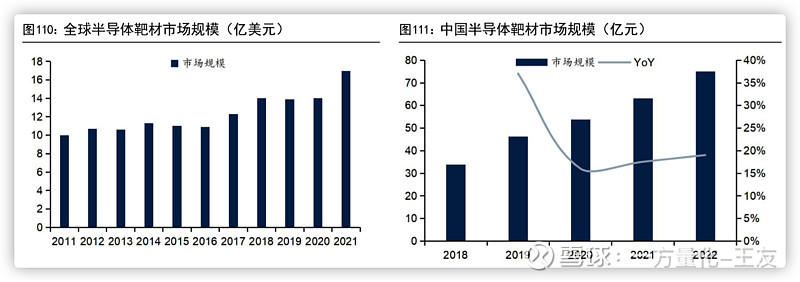
靶材在晶圆制造与芯片封装中均有应用。在晶圆制造过程中,靶材主要用于晶圆导电层、阻挡层的沉积以及金属栅极的溅镀,在封装过程中主要用于贴片焊线过程中的镀膜。其中铜靶、铝靶常作为导电层,钽靶、钛靶常作为阻挡层,镍铬合金靶、钴靶、钨钛合金靶等常作为接触层。
铜、钽靶材受益于先进制程发展,铝、钛靶材受益于汽车电子发展。在晶圆制造过程中,在 110nm 以上的技术节点,常以铝和钛作为一组导电层和阻挡层来使用,进入 110nm 以下的技术节点后,出于对更高导电性能的要求,用铜替换铝作为导电层,用钽替换钛作为阻挡层。因此,先进制程的发展将刺激铜靶、钽靶的需求量增加,而汽车电子所需的功率芯片通常 110nm 以上制程即可满足,铝靶、钛靶将受益于汽车电子发展。
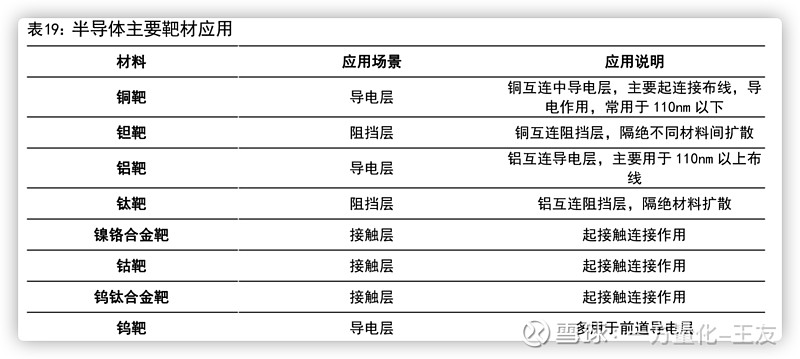
靶材市场主要被世界巨头垄断,国产公司成长迅速。由于溅射镀膜工艺起源于国外,国外靶材公司相较于国内拥有更长时间的成长历史和技术积淀,在靶材市场处于主导地位,根据华经产业研究院数据,截至 2021 年,美日头部靶材企业占据 了全球市场的 80%,其中 JX 日矿金属、霍尼韦尔、东曹和普莱克斯分别占比 30%、20%、20%和 10%。国内企业虽然处于国产替代初期,但头部厂商成长迅速,目前江丰电子、有研新材、阿石创、隆华科技、映日科技等在下游各领域头部企业均打开了一定市场。
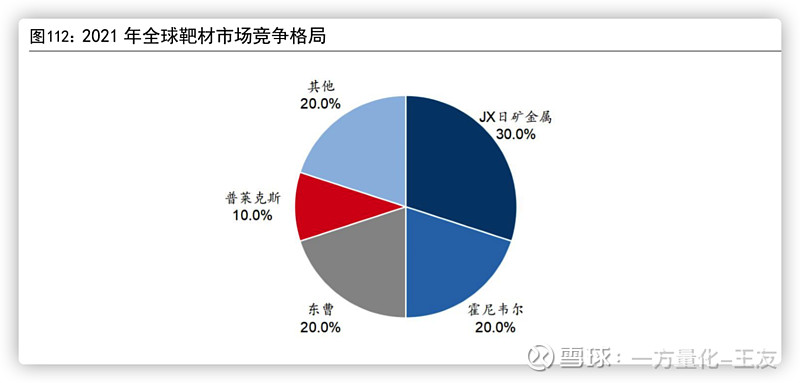
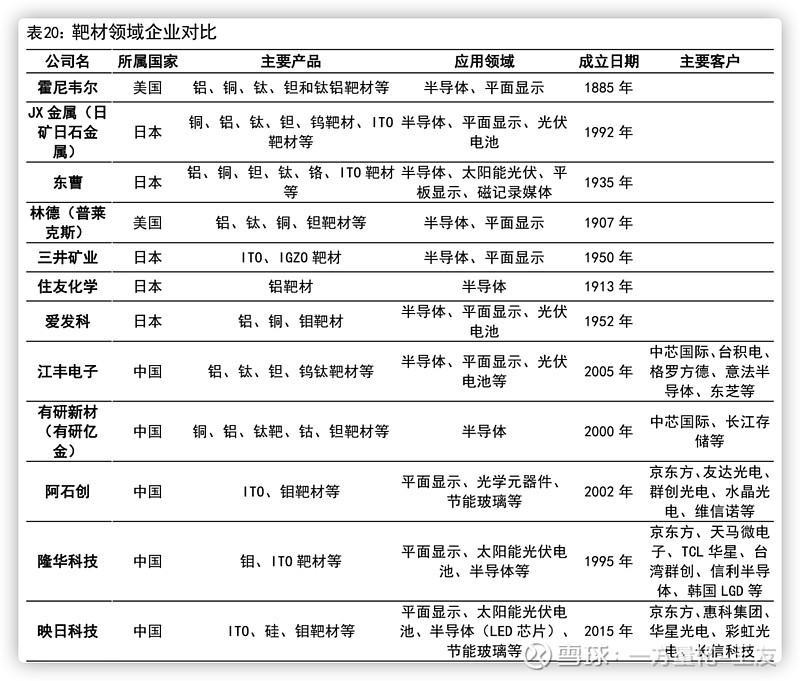
国家政策推进靶材发展,推动靶材国产化。近年来,国家不断出台新的政策法规,来推动靶材行业国产化的发展,特别是集成电路产业的靶材国产化。2021 年颁布的《“十四五”规划和 2035 年远景目标纲要》中,重点提到了集成电路攻关方面,高纯靶材为重点攻关方向之一,国家政策的大力扶持进一步助力靶材产业的国产替代发展。

半导体概念股
我会在 公众号:海涵财经 每天更新最新的医疗新基建、一体化压铸、 汽车智能化,激光雷达,HUD,车规芯片,空气悬挂、L3级智能驾驶、PET铜箔,纳电池,800V高压,光伏HJT、TOPCON、钙钛矿、光伏XBC、BIPV、IGBT芯片、碳化硅SIC、CTP/CTC/CTB电池、4680电池、工业母机、海风柔直高压、新能源车高压快充、高镍三元、碳纤维、PET铝箔、PET铜箔、空气源热泵、新材料、中药创新药、中药配方颗粒、乡村振兴、锂矿、钒液流电池、钠离子电池、分布式储能、集中式储能、抗原检测等最新题材热点挖掘,未来属于高预期差的结构性市场,把握核心赛道以及个股的内在价值逻辑预期差才是根本所在。
— END —
先赞后看,养成习惯
免责声明:图片、数据来源于网络,转载仅用做交流学习,如有版权问题请联系作者删除